Minimiza el número de errores de tu producción y no te pierdas las últimas noticias y avances en Automatización. Suscríbete y sé el primero en enterarte. ¡Únete hoy mismo!
Automatización Industrial
Minimiza el número de errores de tu producción y no te pierdas las últimas noticias y avances en Automatización. Suscríbete y sé el primero en enterarte. ¡Únete hoy mismo!
SuscríbeteConoce nuestros Casos de éxito
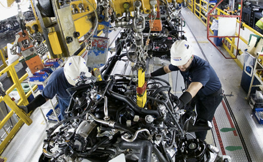
Nuevos controladores ahorran 1 millón de kilovatios-hora cada año y apoyan la eliminación de emisiones. Como resultado, la planta logró recuperar la inversión en nuevos controles antes de los 2 años que se habían estimado.
Conoce nuestros
productos de
Automatización en nuestro
catálogo en línea
En Risoul contamos con un equipo especializado en resolver problemas de Automatización
Más informaciónPlanta de motores reduce costos energéticos con nuevos controladores para compresores de aire
Nuevos controladores ahorran 1 millón de kilovatios-hora cada año y apoyan la eliminación de emisiones
Autor: Rockwell Automation
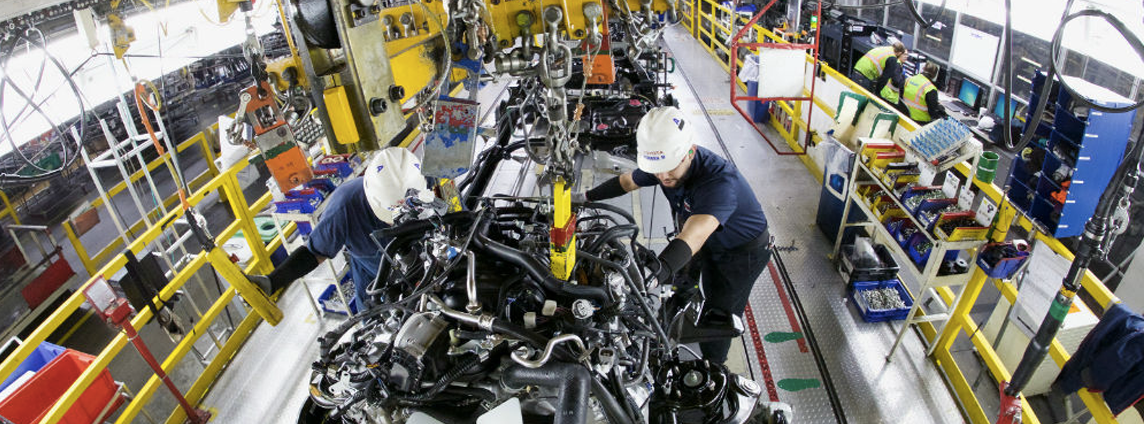
SOBRE LA EMPRESA
Fabricante de motores para vehículos populares. Los trabajadores de la planta reciben componentes de motores que han sido moldeados en otras instalaciones, y su tarea consiste en maquinar y montar estos componentes en los motores que a su vez se instalarán en vehículos de otras instalaciones.
RETOS
El sistema de compresión de aire resultaba vital para su proceso de producción, representando el 25% de los costes energéticos de la planta de motores.
Su meta ambiental era la eliminación de las emisiones de CO2 de sus plantas de producción globales para el año 2050.
NUESTRA SOLUCIÓN IMPLEMENTADA
Para ayudar a reducir los costos energéticos y apoyar su iniciativa de energía de 2050, se decidió actualizar los sistemas de control de los compresores de aire de la planta.
Para ello, se requirió de un socio fabricante de máquinas del programa PartnerNetwork de Rockwell Automation. La empresa proporcionó una solución compuesta de dos partes que abarcó los controles locales y en toda la planta.
Localmente, se migró los controladores de los cinco grandes compresores a su solución de control AirLogix. La solución se basa en la plataforma de control CompactLogix e incluye una interface de operador PanelView Plus 7 que brinda a los trabajadores datos de rendimiento y diagnósticos provenientes de cada compresor.
En el nivel de la planta, se implementó su solución de distribución de cargas para crear un sistema maestro de control de aire. Esta solución está basada en la plataforma ControlLogix aprovecha el software FactoryTalk View SE para recolectar y visualizar datos. También se instaló un tanque de almacenamiento de 19,000 litros para proporcionar aire comprimido reforzado de 500 PSI para permitir que el sistema se recupere antes de entrar en fallo.
Adicionalmente una válvula moduladora suministra aire durante los períodos pico de demanda de aire. Este aire almacenado permite una transición sin interrupciones cuando se requiere una máquina centrífuga adicional a fin de satisfacer la demanda de la planta.
Mayores ahorros
Los nuevos y más eficientes controladores para compresores de aire han permitido que la planta reduzca el consumo de energía anual en casi 1 millón de kilovatios-hora cada año. Además de los ahorros obtenidos por no efectuar arranques durante las horas pico de uso. Como resultado, la planta logró recuperar la inversión en nuevos controles antes de los 2 años que se habían estimado.
CARACTERÍSTICAS DE LOS EQUIPOS UTILIZADOS
-
PLC CompactLogix - Brinda equipos y programas para aumentar la eficiencia de los cincos grandes compresores de aire centrífugos de la planta.
-
PLC ControlLogix - Permite que los compresores compartan las cargas y consuman aire almacenado proveniente de un nuevo tanque de refuerzo.
-
Software FactoryTalk View SE - Permite que los trabajadores de la planta y los socios remotos tengan acceso a información de sistemas prácticamente en tiempo real.
BENEFICIOS
-
Reducción de costes energéticos: Los controladores más eficientes y el acceso al aire almacenado ayudaron a reducir el consumo de energía en casi 1 millón de kilovatios-hora o aproximadamente 68,000 dólares cada año.
-
Mantenimiento mejorado: Los datos de tendencias en tiempo real brindan a los trabajadores visibilidad del rendimiento del sistema y facilitan la resolución de problemas. El acceso remoto permite a los OEM resolver rápidamente problemas online sin necesidad de enviar personal al sitio.